COMPANY
For over 50 years Sepam has been machining aluminium parts for the automotive and industrial fields. Die-casting, gravity casting and forging raw parts are used to manufacture our products.
We supply finished parts to the world’s leading automotive and industrial companies.
We manage directly the whole production process, up to the delivery to the customer: supplier’s selection, raw part purchasing, machining, leakage tests, washing, assembly of components and surface treatments.
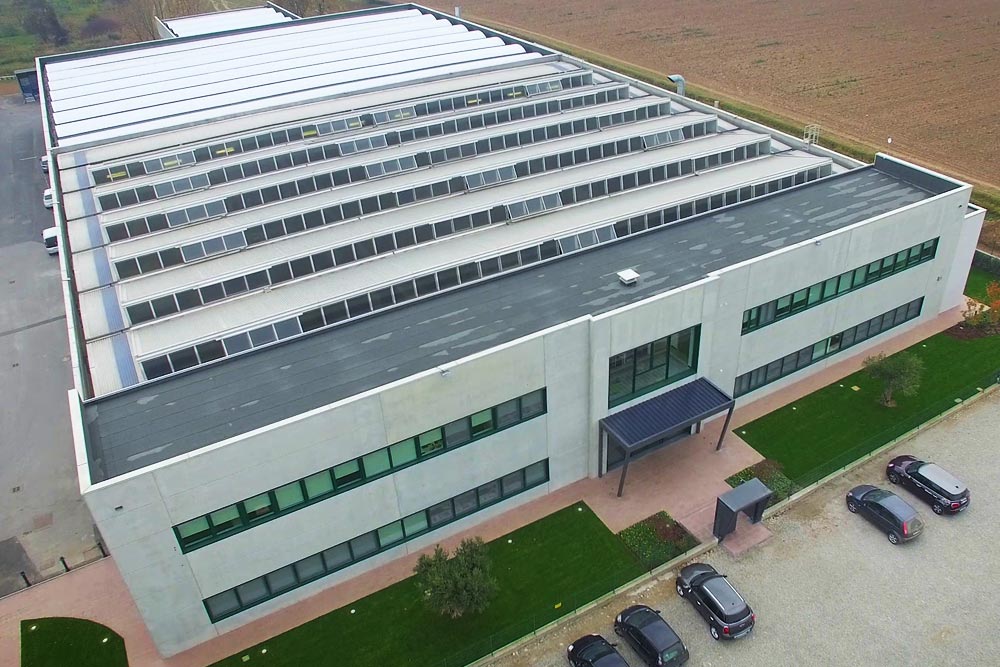
HISTORY
Sepam climbs the supply chain, starting supplying its customers with finished products, taking over the management of sub-suppliers, both of castings and of heat and surface treatments. At the same time a strong increase of export turnover occurs.
First integration of a leakage test station in a line. Today 8 leakage test benches are in operation
Implementation of a Quality System according to the specific requirements for “Safety and Critical Products” as per guideline “Product Safety Audit” of company Knorr-Bremse.
Services
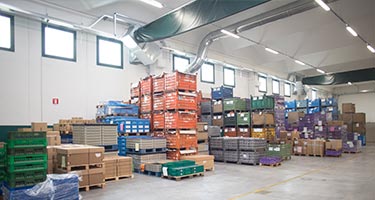
Procurement
Sepam selects only certified and qualified suppliers. They are constantly monitored during all project development and implementation steps.
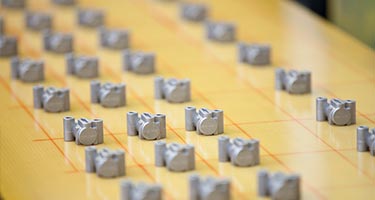
Production
Sepam manufactures complex products by means of lean and state-of-the-art processes.
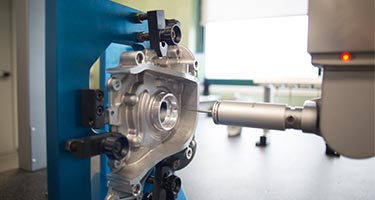
Quality
Sepam performs stringent controls during all production process steps.
Our Quality System is certified according to IATF 16949:2016 and UNI EN ISO 9001:2015.
SOCIAL RESPONSIBILITY
For over 50 years Sepam has been manufacturing machined aluminium parts for the automotive and industrial fields, with expertise and transparency, considering ethical principles as an essential part of its policy.
Our code of ethics represents the guideline both for stakeholders and employees.

Sustainable investments 4.0 (Decree of the Minister of Economic Development 10 February 2022 | Directorial Decree 12 April 2022) – Protocol IS0109934 CUP C85H23001380008
On 17/02/2023 Invitalia admitted the application presented by Officina Meccanica Sepam srl for the granting of the benefits provided for the Sustainable Investments 4.0 tender (Decree of the Minister of Economic Development 10 February 2022 | Directorial Decree 12 April 2022) – Protocol IS0109934.
The operation carried out is composed by the following investments:
Nr.1 automated machining cell composed of 2 CNC machining centers with 5-axis table – 2 CNC lathes – 2 robots, Nr.1 automated washing-leak test and visual inspection cell composed by 1 test bench sealing and 1 washing and sealing testing robot, Nr.1 Profilometer, Nr.1 automation of machining cell, Nr.1 washing machine.
The aims were to respond to the production, technological and sustainability needs of the market through innovative investments that allow the technological and digital transformation of the company, through the use of technologies relating to the Industry 4.0 plan.
The expected and achieved results were:
- higher control over the operation of the machines which will allow to the operetor to work in complete safety environment, avoiding urgent interventions during the production phases and optimized production cycles, evident in the number of operating hours for a given production level;
- better monitoring of machine productivity, planning of work activities, with consequent increase in product quality, reduction of waste and throughput times;
- lower energy consumption through to highly technological systems and the optimization of work spaces.